Recycling Electric Car Batteries
Partially driven up by high gasoline prices, more consumers are purchasing all-electric cars. In fact, electric car sales were up an astounding 65 percent last year. As more and more people drive green cars, recycling the old batteries becomes an important factor. Lithium-ion batteries contain toxic materials and can even catch fire if they aren’t disposed of properly.
Up until now, automakers have been pouring billions of dollars into new EV manufacturing but have been lagging behind on the recycling of EV battery packs. Traditional methods of breaking down old batteries is expensive. The process of pyrometallurgy involves burning old batteries in a furnace to retain their cobalt and nickel. Hydrometallurgy reclaims expensive metals in batteries by using chemistry, but in order to do so, the batteries have to be broken down into tiny bits. Both of these processes only recycle a small percentage of the precious metals in the batteries.
All this is about to change as new lithium-ion recycling facilities are sprouting up around the country. They are making battery recycling environmentally-friendly and extremely profitable. Here is a sampling of what these companies are up to.
EV Battery Recycling Companies
The folks at the American Battery Technology Company (ABTC) have found a way to reverse the manufacturing process of battery packs. Because they are experts at building lithium-ion batteries for Tesla, they know their way around putting them together and taking them apart. While working for Tesla, Ryan Melsert had to find recycling companies who could dispose of waste from building batteries. He was met by a vast void and decided to start his own company.
Using manufacturing machines in reverse, ABTC breaks down the battery packs to its cells, then takes apart the cathodes, anodes, and separators. The process yields more recovered materials for future batteries.
Another company called Li-Cycle in Arizona noticed that traditional lithium-ion battery recycling facilities recover nickel and cobalt but get rid of the lithium used in EV batteries. The company breaks down old batteries in an extremely efficient manner. They submerge the batteries in a solution before sifting out the copper, aluminum and plastic to be used again. Their goal is to use as much recovered material as possible to make recycled battery materials cheaper than mining new materials.
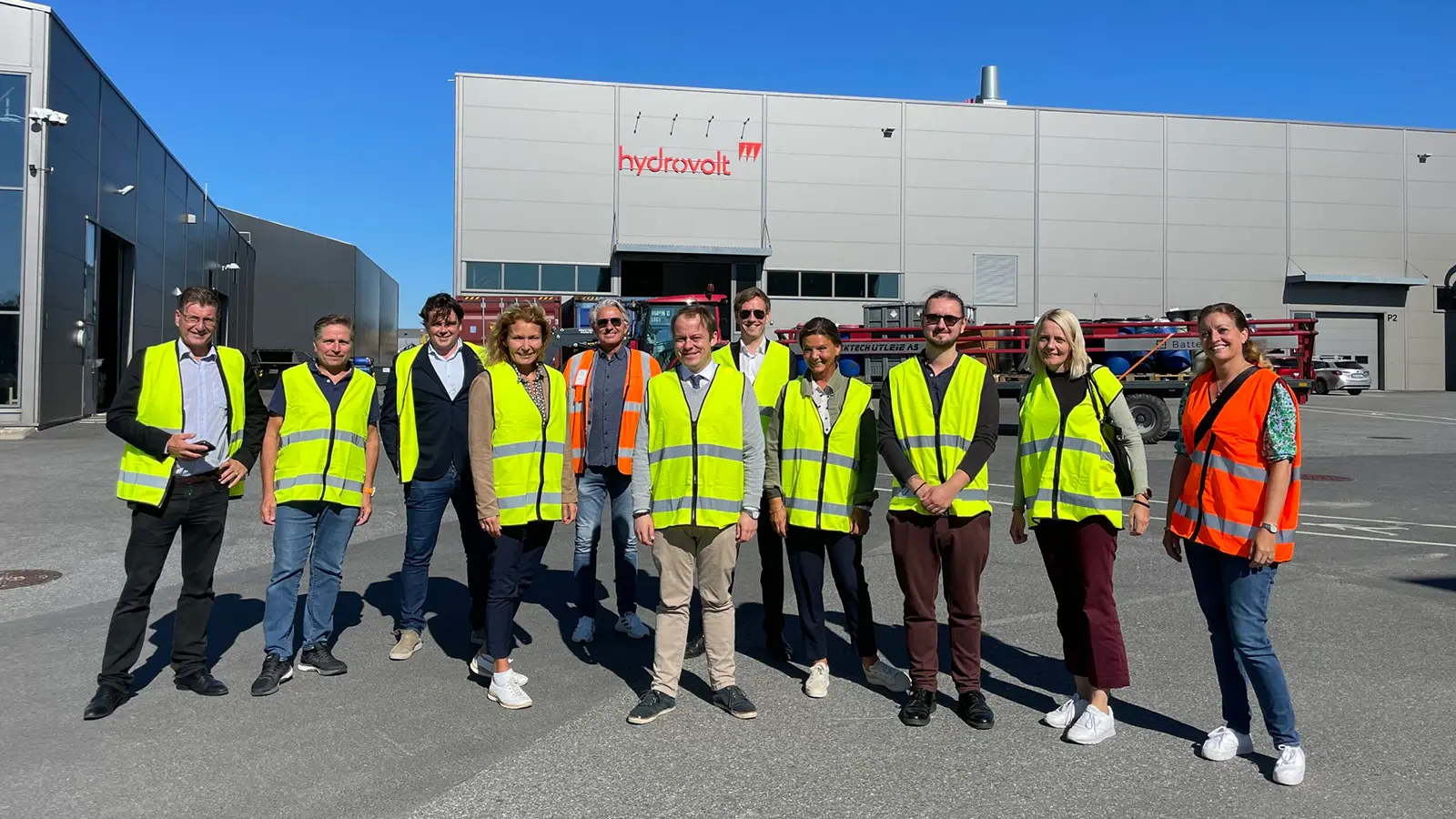
Meanwhile, in Norway, a company called Hydrovolt is Europe’s largest battery recycling facility, turning 12,000 tons of used battery packs into 25,000 new EV batteries. The fully automated process recovers 95 percent of battery materials, including lithium. The plant even captures the dust produced during the process to extract every particle of the rare materials.
Hydrovolt hopes to recycle 70,000 tons of battery packs by 2025.
A company called Ascend Elements out of Michigan is recapturing the most expensive part of used batteries, the cathode. Made from the highly rare, mined materials lithium, nickel, manganese, and cobalt, the challenge in cathode recycling is getting these materials back out of the battery in a usable form.
The company uses a process called hydro-to-cathode in which they shred used batteries and place them in a solution that dissolves the cathode ingredients in their pure atomic state. Ascend Elements uses microstructure engineering techniques to adjust the elemental crystal structure of new cathode material and recover 98 percent of critical elements in used lithium-ion batteries. The process produces cheaper battery materials than mining and refining. In fact, a recent study found that Ascend’s recycled materials outperforms the commercially available equivalent. The company says its carbon footprint is 90 percent lower than companies who manufacture cathode material from virgin sources.
Ascend is building a plant in Georgia to pull recycled materials from used batteries and another facility that will turn the materials into new cathodes, with hopes to be operational by 2024.